Checking Out Advanced Tools and Techniques for Accurate Welding Examination
In the world of welding assessment, the quest of precision and reliability is extremely important, spurring the growth of advanced tools and methodologies. Laser scanning technologies and computerized examination systems, geared up with fabricated intelligence, are redefining the landscape by lowering human error and enhancing safety and security measures.
Ultrasonic Examining Technologies
Ultrasonic testing technologies regularly represent the forefront of innovations in welding assessment technologies. These technologies have considerably enhanced the capacity to identify and examine stoppages within bonded frameworks, making sure improved stability and safety.

Furthermore, innovations in software application algorithms for data evaluation have actually enhanced the precision of defect detection and sizing. Automated ultrasonic testing systems now supply high-resolution imaging, allowing in-depth assessments of weld quality. These systems are usually integrated with sophisticated visualization tools, which promote the analysis of results.
Radiographic Assessment Strategies
While ultrasonic screening developments have established a high requirement in non-destructive assessment, radiographic assessment techniques continue to play an essential function in welding inspection by providing special understandings into material stability. Radiographic screening (RT) employs the use of X-rays or gamma rays to permeate materials, developing a radiograph that visually stands for the inner structure of a weld. This imaging capability is invaluable for detecting subsurface problems such as porosity, additions, and splits that may not show up through surface examinations.
The procedure involves positioning a radiation resource on one side of the weld and a detector on the contrary side. Variants in material density and thickness affect the depletion of the rays, producing a contrasting picture that exactly defines problems. RT is specifically advantageous for evaluating thick areas and intricate geometries where various other methods may fail.
In spite of its effectiveness, radiographic assessment needs to be carried out with rigorous adherence to security methods as a result of the harmful nature of ionizing radiation. In addition, the analysis of radiographs calls for experienced employees, as the top quality of the analysis directly impacts the dependability of the examination. Recurring innovations in electronic radiography are enhancing photo clarity and analysis efficiency, reinforcing RT's essential duty in ensuring weld high quality.
Laser Scanning Advancements
Accepting laser scanning technology in welding examination has reinvented the evaluation of weld top quality and stability. This sophisticated method offers a non-contact, high-resolution methods of capturing thorough 3D information of weld surfaces. Unlike traditional assessment strategies, laser scanning offers fast data purchase, considerably enhancing the efficiency and accuracy of weld examinations. The modern technology uses laser beam of lights to produce precise 3D versions, which are crucial for in-depth analysis of weld dimensions, surface area abnormalities, and potential issues.
Laser scanning developments have caused substantial enhancements in identifying and discovering surface area imperfections such as porosity, absence of fusion, and undercuts. The high-resolution information makes it possible for examiners to do detailed analyses, making sure that welds meet rigorous market criteria. This technique supports the development of digital records, helping with long-lasting quality guarantee and traceability.
In addition, laser scanning technology incorporates seamlessly with software services developed for automated defect discovery and evaluation. The resultant information can be conveniently shared and examined, promoting collective decision-making processes. As sectors remain to demand greater requirements for weld quality, laser scanning continues to be at the leading edge, offering exceptional accuracy and efficiency in welding examination.
Automated Assessment Equipments
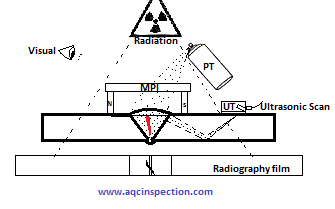
Automated assessment systems provide the benefit of uniformity, getting rid of human error and subjectivity from the assessment process. They are designed to operate in different atmospheres, from production floors to remote field websites, making certain detailed coverage. Welding Inspection Madison. These systems can be configured to follow specific welding criteria and requirements, giving in-depth reports and documents for quality assurance purposes
Moreover, the assimilation of cloud-based platforms helps with the storage and analysis of huge amounts of examination information. This allows pattern evaluation and anticipating upkeep, permitting producers to address possible problems before they intensify. The fostering of computerized inspection systems is an essential relocation in the direction of improving the reliability and effectiveness of welding processes in industrial applications.
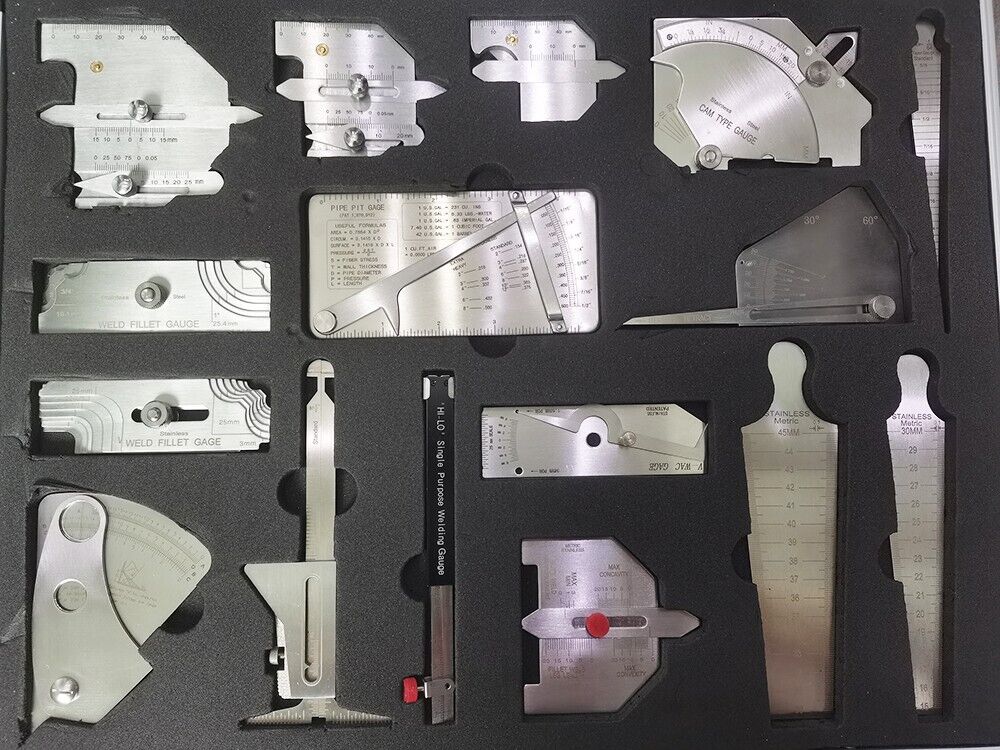
Enhancing Safety and Efficiency
A significant facet of enhancing safety and performance in welding assessment depends on the integration of innovative modern technologies that streamline procedures and mitigate threats. The adoption of advanced non-destructive testing (NDT) approaches, such as ultrasonic screening, phased selection ultrasonic testing (PAUT), and radiographic testing, plays a pivotal role in making sure structural stability without jeopardizing the security of the personnel included. These techniques permit thorough evaluations with minimal downtime, lowering potential hazards linked with standard techniques.
Furthermore, the application of real-time data analytics and artificial intelligence algorithms has actually changed the means assessment information is interpreted. By using anticipating analytics, possible defects can be recognized prior to they materialize right into important failings, making sure prompt interventions and maintenance. This aggressive method significantly improves operational efficiency and safety in welding procedures.
Moreover, remote inspection innovations, including drones and robot crawlers outfitted with high-resolution electronic cameras, make it possible for assessors to evaluate hard-to-reach areas without subjecting them to dangerous problems. This not just enhances evaluation accuracy but likewise lessens human threat. By leveraging these sophisticated tools and approaches, markets can attain greater security requirements and functional performance, ultimately bring about even more trusted and lasting welding evaluation methods.
Verdict
The assimilation of advanced tools and approaches you could try this out in welding inspection substantially improves flaw detection and makes certain structural honesty. These improvements not only raise assessment efficiency but also add to improved safety and web link quality guarantee in commercial welding applications.

Ultrasonic testing developments regularly represent the leading edge of improvements in welding assessment technologies.While ultrasonic screening technologies have established a high standard in non-destructive evaluation, radiographic evaluation techniques continue to play an important duty in welding assessment by offering distinct insights right into material honesty.Embracing laser scanning modern technology in welding evaluation has changed the evaluation of weld quality and integrity. As markets continue to require higher standards for weld quality, laser scanning remains at the leading edge, supplying unequaled precision and effectiveness in welding examination.
Automated inspection systems use the advantage of uniformity, getting rid of human error and subjectivity from the assessment procedure.